Revolutionizing Quick Service Restaurants: A Journey Through Subway's Lean and TQM Operations
- Christine Marion
- Oct 6, 2023
- 13 min read

Quick Service Restaurant and its Operations
The most important thing for a quick service restaurant is always the customers satisfaction. This can be achieved through customer service that is superior. Operations in a Quick Service Restaurant has its differences from the operations of the manufacturer sector. Quick service restaurants serve meals that needs to be consumed and they are prepared and served to the public for profit. Production may have constant change compared to Manufacturing operations as in the QSR operations, demand for food may vary depending on the days in the year, events happening, and menus might change every morning. It is important for the industry to have a goal to achieve a high level of satisfied customers, this can be achieved through great customer service. The success depends on the quality of service, satisfaction of customers, and value. (Chow et al., 2007)
Operations of Subway
Subway is a franchise that performs well globally. Most of the franchises are located in America, but they are available in various locations, as well as Philippines. It is one of the largest fast food chains globally competing with other big fast food chains such as McDonalds. The main goal of Subway is to become number one in the Quick Service Restaurant category worldwide, while having the same freshness of their product as they are known for that. The company gives high quality fresh products are salt reduced, calorie reduced and labeled, and other benefits that most QSR’s do not have. They give the freshest ingredients and the product is made on the spot while the customer is ordering. The products that they offer are mainly sandwiches, salads, breakfast, soups, and desserts. Their mission statement is “to delight every customer, so they want to tell their friends— with great value through fresh, delicious, made-to-order sandwiches, and an exceptional experience.”
The operations of Subway start with keeping track of inventory. The ingredients and materials needed is prepared beforehand. The freshness of ingredients is due to ingredients being cut before the opening time. The ingredients are placed in bins in the assembly line where the customers can also see the preparation. The amount of raw ingredients prepared is based on what is popular among customers. Their facility is basically having a small space wherein the oven and refrigerator are near to the sandwich making station and the cash register. This makes it efficient if there are only 3 employees in one franchise, as they can switch roles easily, and make things faster.

As seen in the figure above, the chief executive is the highest post in Subway. All the huge decisions that decide the company’s standing will be made by the chief executive. Under the chief executive is the functional manager who are the ones in-charge of making sure the positions under them are doing their job accordingly to their tasks to achieve the goal. Manager of Project Managers are in the same level as functional managers, but the manager of project managers are the ones supervising the project manager under the supervision. Each branch of Subway has their own project managers. They are the ones in-charge of the staff. They report to their own managers for reports.
Planning, Organizing, Staffing, Directing, and Controlling are some of the basic management functions that are used by all the managers in the organization. Planning is needed to reach the main objective of the franchise, or the whole organization. Organizing is grouping the necessary actions or activities in a logical way. Staffing is determining what kind of quality staff is needed, and all about the staff’s performances. Directing is helping the staff and guiding them on what to do. Controlling is concerning the actions that has been done questioning whether it is aligned with the plans. (Krishali, 2015)
Matrix management system is being used by subway as they are a huge chain, so with the matrix management system, dual reporting system is used against the traditional way. There is a hierarchy in the organization that divides all the leader’s tasks.
There are three main key approaches to operations management. These are Lean Management, Six Sigma, and TQM.

Lean Management
Lean Management is a methodology that eliminates waste, but still adds value. Its aim is to satisfy customers, while getting rid of unnecessary factors that increases cost, or prolongs the process of giving service to customers. It is the approach to directing a company or an organization that has the aim to implement the idea of continuous improvement. It is a long-term way to approach work that wants to achieve small, incremental changes in the processes of the organization, to upgrade the efficiency and quality. Productivity is not sacrificed in Lean Management even if its goal is to minimize waste activities. Its goal is basically to create more value for the consumers without increasing costs. Lean management can be applied in different operations such as manufacturing and quick service operations. Lean management applied to quick service is quite similar, but different in some aspects. The main difference is that in quick service, fast food is usually produced and needs food preparation before serving customers, while in manufacturing, when it is delivery time, the product is already made.
The approach to directing a company or an organization that has the aim to implement the idea of continuous improvement is called Lean Management. It is a long-term way to approach work that wants to achieve small, incremental changes in the processes of the organization, to upgrade the efficiency and quality. Productivity is not sacrificed in Lean Management even if its goal is to minimize waste activities. Its goal is basically to create more value for the consumers without increasing costs. Lean management can be applied in different operations such as manufacturing and quick service operations. In Manufacturing Operations that uses lean management, it helps the manufacturing operations to become more organized, therefore, minimizing the time being used, and all the unnecessary steps that makes the process longer. Toyota developed this idea by having the Just in Time model (JIT), that has the aim to have a flow of materials with minimal inventory. It is also a pull system which adjusts to the demand of customers, therefore, not wasting materials. JIT is implemented by a Kanban system. A Kanban system is basically a way of controlling the production in the right quantity and the right time, therefore, orders are delivered on time, increasing value of customer. Kaizen is applied to Lean Manufacturing as its main goal is to have efficiency. Lean management applied to quick service is quite similar, but different in some aspects. The main difference is that in quick service, fast food is usually produced and needs food preparation before serving customers, while in manufacturing, when it is delivery time, the product is already made. Another difference is it is easier to transport products from the location production is happening when it comes to quick service. It is because each store has specific numbers of products needed.
The concept of lean management applies to Subway as they remove unnecessary steps, and steps that produces waste. An example of application of lean management at Subway is that they make the sandwich the time when it is just ordered by a customer. It reduces waste as overproduction of sandwiches will be avoided. This process is called single piece flow, which gives customers customization to their orders, while having a fast production. Another process in Subway that is part of the lean management is their policy “order first, pay late” which reduces the time, therefore, increasing efficiency of production. Fresh ingredients are in a pull system, which minimizes the waste that Subway makes as they take note of what is popular, and increases raw ingredients for the popular ones. JIT process is also applied as the inventory is reduced, and products are made on the spot. The Kanban and Pull system way of approach is also applied in Subway through the inventory. There is a certain amount of level per ingredient, and if that level is reached, it will be replaced with a new batch.
Six Sigma
Six sigma has the goal to do a certain process continuously and by doing it, it improves the process, so it will achieve the goal to produce an output that can be predicted, consistent, and stable. The goal of six sigma is to reach a six-sigma level, meaning there will be only 3.4 defects for every one million tries. One standard deviation is equal to one sigma. There are two methodologies used in six-sigma: they are composed of 5 sections in the 2 methodologies, DMAIC and DMADV.
When improving the process of the business, DMAIC is used. It stands for; D, as defining the problems and goals; M, measure details of aspects in the process; A, analyzing data to find defects in process; I, improving the process; and C, controlling the future of the process. For creating new processes, products, or services, DMADV is used. It stands for; D, defining the goals; M, measuring component of process; A, analyzing data and developing design; D, designing, and testing the components; V, verifying the output by doing simulation, before giving it to the customer.
TQM
Total quality management is done thru customer satisfaction to achieve the long-term success. The main point of TQM is that it is customer focused. The level of quality is determined by the customers. The feedbacks of customers are the basis whether anything that an organization is doing is worth the effort. Employees are highly involved in this methodology. Everyone is working to achieve a common goal. The process is also a highlight in TQM. Its importance is that the main focus of this approach is all about customers, so surveys, and charts, are always involved as this is how to measure the satisfaction of customers.

Improvement to Operations to Achieve Business Objectives
With the help of the key approaches mentioned above, the efficiencies of the operations of an organization is improved in many ways such as decrease of waste, less time to produce products, less cost, and better service for customers. The leaders and managers can start by applying lean management as this is the most commonly used approach of leading QSR globally, some of them are McDonalds, and Burger King (Muller, 2012). It minimizes waste, but adds value to the company. Leaders and managers can start by analyzing which areas of operations can be changed to make it more efficient, like in Subway, they implemented the one-piece flow process, progressive production, “order first, pay late” concept, JIT process, along with the Kanban system.
Consultative Leadership is the most appropriate type of leadership to successfully make the operations more efficient to achieve the business goals. This leadership is a combined autocratic and democratic style, meaning manager’s are the ones who will handle big decisions, while employees can do their own decision making on a smaller scale (Olar, 2018) To successfully apply the key approach for operations, the leader and manager should communicate with the staff with all the systems that they think makes the process of creating a product takes time, with this, managers and leaders can research or think of ways to lessen the time of production. It will make the service faster and more efficient. After this, the managers and leaders would inform the staff of the changes the managers and leaders made. When there are problems that might occur during their service regarding customers, the staff can make their own decisions, but still following the ethics of the business, as this will lessen the time because it will add time when the staff will inform the manager and the manager will think of the solution.
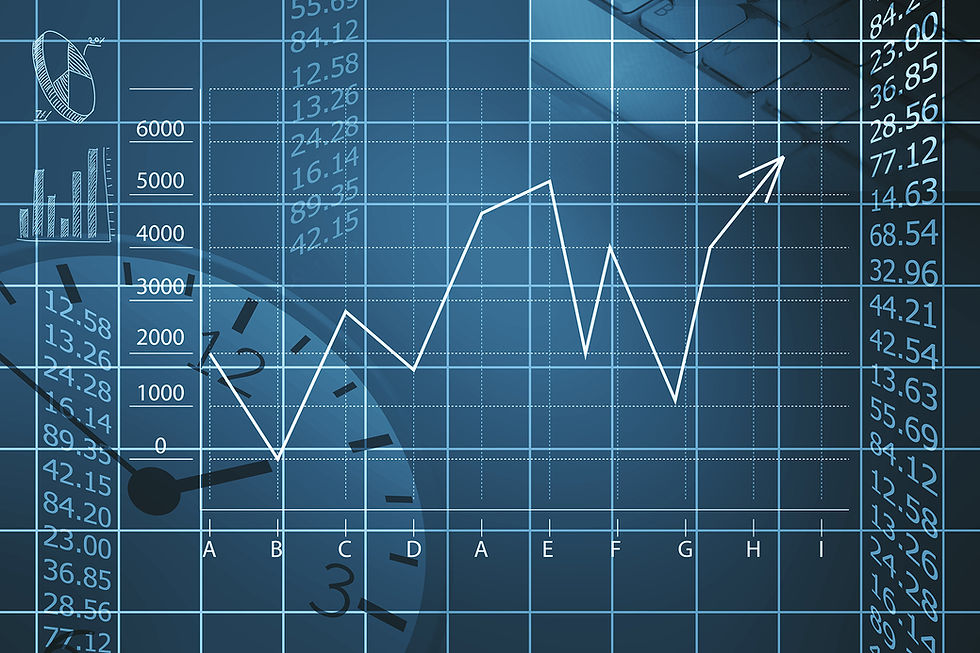
Environmental Factors that Affects a QSR Business
Decision-making is part of being leader or a manager, and they are the ones who can influence the people who are under them. The decisions that managers and leaders make are affected by the external factors. Decision making is a way for effective management and leadership as it is a critical that a leader or manager should possess. A person is not suited to become a leader if they the ability to make decisions for the team or for themselves. External factors are basically the Political, Economical, Social, Technological, Legal, and Environmental factors that can affect a business. The decisions that managers or leaders make are not exempted from being affected by external factors. Mainly, the external factors that affect the decisions of managers and leaders are the market or industry of the organization, the economy, government legislation, and customers feedback. First, changes in the QSR industry can affect the decision-making as the industry changes constantly based on innovations, trends, competitors, legislation, environment, and the economy of QSR or its growth domestic product. New innovations can affect the decision-making of a manager or a leader as these new innovations can be a way for a company to increase its efficiency based on its operations especially when it makes a process easier and faster. For competitors in the industry affecting the decision-making of managers and leaders, it would make them think of ways to compete with them and keep on rising and growing as a business.
Companies use the growth domestic product to predict their business growth. This external factor can help a manager or a leader as circumstances such as the GDP falling, the manager or leader can decide to save extra cash for backup, meaning cutting cost to prepare. If the GDP is increasing, the managers or leaders can choose to expand by hiring new employees, pay higher salaries, promote more products, and ways to expand the business. An environmental factor can also affect the economy, and the economy of a specific industry. The government enforced people to do quarantine and this is due to the virus, and it affects the economy as well.
Customers feedback is also one of the most important external factors that can affect a manager or leaders’ decisions. A business’ aim is to serve quality products or services to customers that is done efficiently and effectively, so it is important to know what are the customers thoughts about what an organization can offer. Subway can get customer’s feedback by conducting surveys and searching for food blog sites that reviewed their products, operations, and services.
Legislation can affect the operations of a QSR business as there are laws and regulations that QSR businesses that needs to be followed. There is a minimum level of hygiene, customer service, payroll, staff, and storage that needs to be aligned with the business. Legislations are changed at times, and QSR businesses need to follow the changes all the time
Environmental factors can also affect the operations as QSR relies on raw materials, so changes in weather can affect the quality of the product. For Subway, they are known for the freshness of their raw materials, so they need to make sure that they get fresh ingredients from their farm. Subway’s farmers make sure that the meat that they provide are antibiotic-free. They prevent farm animal illnesses by having cleanliness, animal nutrition, and managing techniques for their animals (Patsche, 2015).They are also trying to enhance their menu by trying to remove GMO ingredients and products.
Trends can also affect the operations of Subway as the trends can help the business be unique compared to its competitors. One of the trends this 2020 is definitely restaurants participating in delivery (Gentile, 2019). Using third party delivery services are on trend this year, and Subway also took advantage of this. They are in third part delivery service like FoodPanda in the Philippines and Uber Eats in other countries.
There are also internal factors that can affect the operations of QSR businesses. First weakness that Subway has is the brand value compared to competitors. It does not just apply with Subway but with other QSR. They are suffering in brand value comparing it to the highest in brand value which is McDonalds with $43 billion, next in the rank is Subway with $10.3 billion in 2019 (Bhasin, 2019). The gap between the top 1 and top 2 are very far, as McDonalds stay on top and the second spot is usually changing every year. Another factor that affects the business internally is franchised QSR usually do not have a consistent service satisfaction for stores around the world.
Impact of Business Environment Factor to a Business
All the factors can affect the decision making of leaders as these factors can improve or prevent the operations of a business. For example, if there are new laws that affect a specific business’ operation, the leaders or managers need to find a way to maintain their operations and their processes, or think of ideas to make the operations more efficient like what is in lean management. These factors can either make or break the operations, it can be either give a positive outcome, or a negative one for the business. That is why leaders and managers need to carefully analyze their next move after all these factors are known. Investing in new technology can help the operations to be faster, but it might cost a lot. So, the managers need to question “Will it help to achieve the business’ objectives?”. Researching about the factor affecting the productivity of the business is a great help as it can be used as a guide for the decision that the leaders or managers will do.

Conclusions and Recommendations
The QSR, Subway, is still stable in business as their lean management approach is effective until now. Their small working area makes it efficient for the employees to get to where they need to, making the sandwich making process faster. The way that they serve customers where they let them customize their orders can make it easier to control the inventory. The leader or manager can observe and tally per raw ingredients which ones are frequently picked by customers. The ones that are selling the most should have more inventory specially the lettuce and tomatoes as these two are the basic ingredients in a Subway sandwich. The only problems in relation to ingredients are the environmental factors. It is because there are seasons when the main farm where the ingredients got from do not have fresh ingredients due to the weather. Also, Subway is a franchise, and Subway has the most stores in the QSR industry, so it will be hard to monitor all of them to see whether their ingredients, operations, and processes are on par to the main standard of a Subway store. A way to monitor the quality of each store is all the managers of each store in a certain area shares updates about their stores in a file given to the main manager that manages all the project managers in each area. Also, a surprise inspection for every store can be done to know how a specific store is doing. A recommendation for a solution for having fresh ingredients is always have back-up suppliers internationally and locally for a specific store, if there are quality issues in the main farm suppliers.
The best approach for the operations of any QSR are Lean management and TQM. Both of these approaches can work hand and hand together to have the best operations. Lean management focuses on getting rid of unnecessary steps in production and operations that increases the cost, and TQM focuses on opinions of customers about the speed, quality, ambiance of the restaurant, and other factors (Westcott, 2013). These two approaches can work together as TQM can be a basis for lean management to work basing it to the customer’s feedback. The customers are one of the main priorities of a business, so it is really vital to hear their feedbacks about the serving time, the venue of restaurant, the quality of food, and the performance of the employees. They are the main judges of the restaurant, and they are the ones who are targeted. Without the customers, a business would go bankrupt. So TQM, is also really important, and lean management can adjust to what the customer wants to make the operations faster and be on quality with less cost.
Download presentation deck here:
BIBLIOGRAPHY
Economics Discussion. 2020. What are the Functions of Management? - 7 Functions of Management. [ONLINE] Available at: http://www.economicsdiscussion.net/management/7-functions-of-management/31965. [Accessed 04 May 2020].
The Restaurant as Hybrid: Lean Manufacturer and Service Provider | Boston Hospitality Review. 2020. The Restaurant as Hybrid: Lean Manufacturer and Service Provider | Boston Hospitality Review. [ONLINE] Available at: https://www.bu.edu/bhr/2012/09/01/the-restaurant-as-hybrid-lean-manufacturer-and-service-provider/. [Accessed 04 May 2020].
prezi.com. 2020. Subway & Its Operatinal Management by REMAX 2000 on Prezi . [ONLINE] Available at: https://prezi.com/c13hh48d3tar/subway-its-operatinal-management/. [Accessed 04 May 2020].
Marketing91. 2020. SWOT Analysis of Subway - Subway SWOT analysis. [ONLINE] Available at: https://www.marketing91.com/swot-analysis-subway/. [Accessed 04 May 2020].
The Certified Manager of Quality/Organizational Excellence Handbook, Fourth Edition | ASQ. [ONLINE] Available at: https://asq.org/quality-press/display-item?item=H1447. [Accessed 04 May 2020].
Subway Got Too Big. Franchisees Paid a Price. - The New York Times. 2020. Subway Got Too Big. Franchisees Paid a Price. - The New York Times. [ONLINE] Available at: https://www.nytimes.com/2019/06/28/business/subway-franchisees.html. [Accessed 04 May 2020].
FoodFindsAsia.com. 2020. 4 Leadership Styles to Use for Restaurant Business. [ONLINE] Available at: https://www.foodfindsasia.com/4-leadership-styles-to-use-for-restaurant-business/. [Accessed 04 May 2020].
5 Fast Food Trends to Look for in 2020 | Parts Town. [ONLINE] Available at: https://www.partstown.com/about-us/fast-food-trends-2020. [Accessed 04 May 2020].
(DOC) Subway - Company Analysis | Aiman Hakimi Mohd Sapudi - Academia.edu. [ONLINE] Available at: https://www.academia.edu/38357942/Subway_-_Company_Analysis. [Accessed 04 May 2020].
Comments